Pumpenauswahl
Füllkörper
Füllkörper werden in stationäre und mobile Füllkörper unterteilt, während herkömmliche Füllkörper in Blockdüsen und individuell verlegte Füllkörper unterteilt sind.
Strukturierte Füllkörper sind ringförmig, zylindrisch, sattelförmig, kugelförmig und in anderen Formen erhältlich. Die Verbesserung der strukturierten Füllkörper wird hauptsächlich durch Modifikationen bekannter Konstruktionen erreicht, beispielsweise durch eine Erhöhung der Anzahl von verbogenen Elementen oder durch eine Änderung des Verhältnisses von Höhe und Breite des verpackten Gehäuses.
Die Dichtungskörper der beweglichen Aufsätze sind kugelförmig, zylindrisch, spiralförmig, ringförmig, prismatisch, kubisch, können hohl, hohl oder perforiert sein.
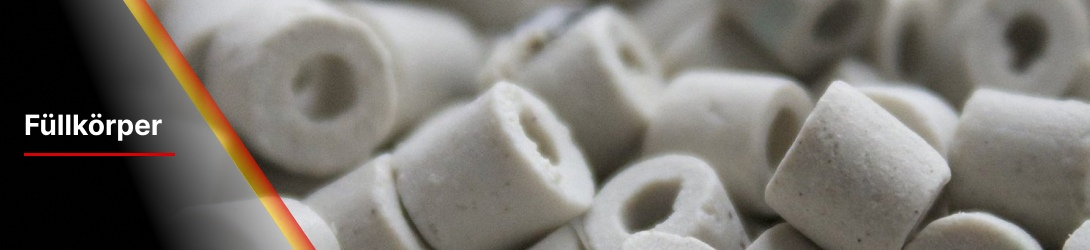
Geräte mit verdichtetem Kontakt als Werkzeug zur Verstärkung von Wärmeaustauschprozessen und Massen an und in der Nähe der Trenngrenze durch Erweiterung der Kontaktfläche und Verbesserung der Strömungsmischung werden in den in der Industrie weit verbreiteten Wärmeaustausch- und Masseaustauschprozessen eingesetzt. Die am meisten angewendeten Prozesse sind die Absorption, Begradigung und Verdunstungskühlung von Wasser. Absorption-Selektive Absorption von Gasen oder Dämpfen durch absorbierende Flüssigkeit (saugfähig). Dieser Prozess, an dem die Gas- und Flüssigkeitsphase beteiligt ist, beinhaltet den Übergang einer Substanz aus der Gas- oder Gasphase in eine Flüssigkeit. Der umgekehrte Prozess ist die Freisetzung von absorbiertem Gas oder Dampf aus dem Absorber – Desorption. Es gibt zwischen physischer Absorption und Chemosorption. Bei physikalischer Absorption wird die Auflösung des Gases nicht von einer chemischen Reaktion begleitet. Bei chemischer Absorption tritt die absorbierte Komponente in der flüssigen Phase in eine chemische Reaktion ein. Im Gegensatz zum Begradigen ist der Absorptionsprozess grundsätzlich einseitig. die entsprechenden Komponenten werden aus dem Gas extrahiert und gehen praktisch nicht vom Absorptionsmittel in die Gasphase über. Eine ähnliche Situation wird bei der Desorption beobachtet. In der Industrie werden der direkte Prozess (Absorption) und der umgekehrte Prozess (Desorption) am häufigsten in Kombination verwendet: Absorption und nachfolgende Desorption. Diese Kombination ermöglicht die Wiederverwendung des absorbierenden Inhaltsstoffs und die Isolierung der absorbierten Komponente in reiner Form. Dazu wird die Lösung nach dem Absorber zur Desorption geleitet, wo durch Entladen oder Erhitzen die absorbierte Komponente freigesetzt wird und der regenerierte Absorber zur Absorption zurückkehrt. In einem solchen zyklischen Prozess wird das Lösungsmittel nicht verbraucht, sondern es zirkuliert ständig im Absorber System. Bei der Chemosorption wird das Absorptionsmittel durch Erhitzen oder chemische Methoden regeneriert.
In der chemischen Technologie wird die Kombination von Absorption und Desorption am häufigsten verwendet, um:
- trennung von Gasgemischen unterschiedlicher Herkunft der Ausgangskomponenten, die dann zur Synthese geliefert werden;
- in der Vorbereitungsphase für die Synthese von Quellgas oder Gasgemischen (Dehydrierung, Entfernung schädlicher Verunreinigungen);
- trennung von wertvollen Komponenten aus einem Gasgemisch, das durch Reaktion oder thermische Zersetzung erhalten wurde;
- entfernen schädlicher Verunreinigungen aus den Abgasen (hygienische Reinigung) mit anschließender Verwendung der extrahierten Substanzen;
- einfangen von wertvollen Stoffen aus Abgasen, um deren Verlust zu verhindern, sowie aus ökologischen Gründen. 16 aus dem Obigen ersichtlich ist, dass die Kombination von Absorption und Desorption als technologischer Vorgang in verschiedenen Phasen von Produktionsprozessen weit verbreitet ist.
In einigen Fällen wird nur die Absorption verwendet (keine nachfolgende Desorption):
- um das Zielprodukt durch Absorption von Gas durch Flüssigkeit zu erhalten;
- um das Gas von unerwünschten Verunreinigungen zu reinigen, wenn das Absorptionsmittel und das Produkt, das Sie extrahieren, Abfallprodukte sind oder so billig sind, dass die Regeneration des Absorptionsmittels wirtschaftlich unpraktisch ist.
In den Absorptionsprozessen, die für die oben genannten technologischen Aufgaben entwickelt wurden, werden hauptsächlich verpackte Kontaktvorrichtungen verwendet. Die Rektifikation wird mindestens als Absorption angewendet. Die Gleichrichtung [7] ist die Trennung eines flüssigen Gemisches in Komponenten durch die Gegenstromwechselwirkung der während der Verdampfung erzeugten Dampfströme und der durch Dampfkondensation erzeugten Flüssigkeit. Dieser Prozess beinhaltet wiederholt wiederholte Übergänge eines Stoffes aus der flüssigen Phase in die Gasphase und umgekehrt. In der Antike war ein einmaliger Verdunstungsakt bekannt, bei dem eine überwiegend flüchtige Komponente in Dampf übergeht und dann kondensiert - Destillation. Er hat eine bedeutende Entwicklung erfahren, als er lernte, Alkohol aus den Fermentationsprodukten von Materialien zu extrahieren, die Stärke und Zucker enthalten. Im Gegensatz zur Absorption erfolgt dieser Prozess während der Begradigung nicht mit jedem einzelnen Akt in dieselbe Richtung. Bei der Verdampfung verdampft zusammen mit der flüchtigen Komponente eine gewisse Menge an nicht flüchtiger Komponente. Daher können Sie mit einer einzigen Aktion kein sauberes flüchtiges Produkt erhalten. Sie benötigen mehrere Wiederholungen eines einzelnen Aktes. Aus diesem Grund sind hohe Energiekosten erforderlich, um die Destillation 17 zu realisieren, viel höher als bei der Absorptionstrennung. Aufgrund der Tatsache, dass das Produkt durch die Auswahl der erforderlichen Anzahl von aufeinanderfolgenden Einzelakten aus der Mischung von ausreichend hoher Reinheit isoliert werden kann, hat die Rektifikation jedoch eine breite Verbreitung gefunden. Der Begradigungsprozess kann periodisch oder kontinuierlich organisiert werden. Bei der kontinuierlichen Rektifizierung von Binärmischungen kann es sich um eine Mischung von Komponenten mit unbegrenzter gegenseitiger Löslichkeit, eine Mischung von Komponenten mit niedrigem Siedepunkt oder eine azeotrope Mischung handeln. Zur Trennung von Mischungen von Komponenten mit niedrigem Siedepunkt wird häufig eine Extraktionsdestillation verwendet, bei der der Zweikomponentenmischung ein dritter Teil hinzugefügt wird - ein Trennmittel, das die relative Flüchtigkeit der Basis der Komponenten erheblich erhöhen kann. Azeotrope Mischungen werden durch azeotrope Destillation getrennt. Am schwierigsten ist das Begradigen von Mehrkomponenten-Mischungen. Es gibt verschiedene Schemata für seine Implementierung.
Die Vakuumdestillation wird verwendet, um thermisch stabile Mischungen zu trennen. Die Rektifikation ist in Branchen von besonderer Bedeutung, in denen flüssige Mischungen vollständig in reine Komponenten oder Gruppen aufgeteilt werden müssen. Für die Realisierung von Richtprozessen werden hauptsächlich Plattenkontaktvorrichtungen verwendet. Die weit verbreitete Verwendung von Dichtungen in Destillationsprozessen ist trotz der Einfachheit der Vorrichtung und der relativ geringen Kosten durch ihre geringere Effizienz aufgrund der ungleichmäßigen Verteilung der Dampf- und Flüssigkeitsströme im Querschnitt der Füllschicht behindert. Daher sind in Chemieanlagen selten Destillationssäulen mit einem Durchmesser von mehr als 2-3 m zu finden. Die Dichtungen sind jedoch für die Destillation von thermisch stabilen Stoffen notwendig, da nur die Netzdichtungen einen sehr geringen hydraulischen Widerstand der Massentransportvorrichtung bieten können, der für die Durchführung des Destillationsprozesses im Vakuum notwendig ist. 18 Kontaktvorrichtungen werden auch häufig zum Kühlen von Gasen mit Wasser und Flüssigkeit (hauptsächlich Wasser) mit Luft oder Gasen (wenn sie mit Kühlmitteldampf gesättigt werden können) mit direktem Phasenkontakt verwendet
Wenn die mit der Übertragung von Wasser aus dem Gas in die flüssige Phase verbundene Trocknung von Gasen gemäß ihrer technologischen Bestimmung vollständig mit Massentauschprozessen verbunden ist, bezieht sich die Luftkühlung, die auch von der Übertragung von Wasser aus der flüssigen Phase in die Gasphase begleitet wird, entsprechend der technologischen Bestimmung auf die Wärmeübertragungsprozesse. Der Wärmeaustausch im direkten Kontakt ist viel effizienter als bei Wärmetauschern, bei denen sich im Gegenstrom bewegende Ströme durch eine Wärmetauscheroberfläche (eine Wand) getrennt sind. Der thermische Widerstand dieser Wand sowie Verunreinigungen, die sich unweigerlich auf beiden Seiten ansammeln, verringern die Wärmeaustauscheffizienz. Es ist sehr wichtig, dass bei direktem Kontakt der Phasen eine erhebliche Menge an Wärme durch Verdampfung eines Teils der Flüssigkeit in die Gasphase abgegeben wird. All dies zusammen sorgt für eine hohe Kühleffizienz. Dies ist jedoch nur zulässig, wenn die Technologie es dem Gas ermöglicht, mit Flüssigkeitsdampf gesättigt zu werden. Diese Sättigung ist für die Verdunstungskühlung des zirkulierenden Wassers in Kühlräumen, in denen regelmäßig befüllt wird, durchaus akzeptabel. Natürlich ist es wünschenswert, dass die Paarung aus zwei Gründen minimal ist. Erstens wird es aufgrund des Verlustes der Wasserzirkulation oft einer chemischen Vorbehandlung unterzogen, um den Salzgehalt der Flüssigkeit zu reduzieren. Zweitens wegen der unvermeidlichen Befeuchtung und Verschmutzung des Luftbeckens im Bereich der Kühltürme. Dazu sind die Kühltürme mit speziellen Geräten ausgestattet, die den Wassertransport durch Tropfen aus den Kühltürmen minimieren.
Bereiche und Anwendungsgebiete chemische Anlagen können von weitem an charakteristischen Stützen erkannt werden. Ihre Höhe erreicht manchmal 100 m, ihr Durchmesser beträgt mehrere Meter. Es ist in ihnen, dass die Prozesse des Massenaustauschs- der Absorption und der Rektifikation - stattfinden. Bei der Gesamtmenge der Verarbeitungsausrüstung von chemischen Anlagen erreicht der Metallverbrauch für solche Geräte in einigen Fällen 60%. Ein Großteil dieser Ausrüstung fällt auf Verpackungsvorrichtungen. Gefüllte Säulen werden in vielen wichtigen Industriezweigen der chemischen Industrie für anorganische und organische Produkte weit verbreitet verwendet. Füllkörper werden derzeit in großem Maßstab in verschiedenen Unternehmen hergestellt. Die führenden Unternehmen in Europa sind: Raschig, Sulzer, Nutter, Balke-Durr, Jamon, etc.; in den USA: Norton, Koch, Masstransfer, Glitch usw. Diese Unternehmen starten nicht nur die industrielle Produktion von Pflanzungen, sondern forschen auch an der Verbesserung bekannter Pflanzkonstruktionen, der Entwicklung neuer Strukturen, dem Erwerb neuer, modernerer Materialien für ihre Produktion usw.